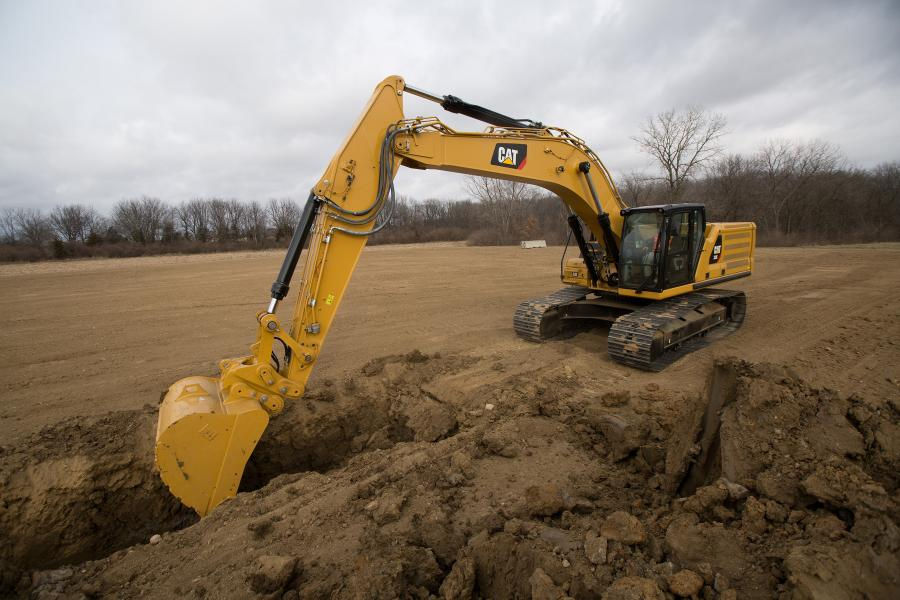
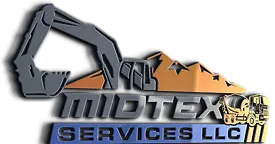
972.880.9459
Frequently Asked Questions
What should the customer know about your pricing (e.g., discounts, fees)?
Our pricing is transparent and designed to offer value to our customers. We believe in simplicity and clarity, ensuring that you understand exactly what you're paying for. There are no hidden fees or unexpected charges. We offer flexible pricing plans to cater to different needs, allowing you to choose the option that best aligns with your requirements. Additionally, we provide detailed information on our quotes. We strive to build trust through fair and competitive pricing, emphasizing our commitment to customer satisfaction.
​
What is your typical process for working with a new customer?
It begins with a thorough understanding of your needs through initial consultations. Once objectives are clear, we tailor solutions to align with your goals. We prioritize transparency, providing detailed timelines and milestones. Our commitment is to establish a lasting partnership, ensuring a positive experience for every new customer.
What types of customers have you worked with?
Throughout my career, I've had the privilege of collaborating with a diverse range of customers, spanning both commercial and residential. In the commercial sector, I've partnered with businesses of various sizes, tailoring solutions to meet their specific operational needs. Simultaneously, in the residential realm, I've worked closely with homeowners, ensuring their individual requirements are met with precision and care. This broad spectrum of clientele has provided me with a comprehensive perspective, allowing me to adapt and excel in delivering tailored services across different customer profiles.
​
Are the terms “concrete” and “cement” interchangeable?
No, the terms "concrete" and "cement" are not interchangeable, although they are often used incorrectly in everyday language. Here’s the distinction between the two:
​
-
Cement: Cement is a binding agent or binder used in construction. It is a fine powder made primarily from limestone, clay, and other minerals that are heated to a high temperature in a kiln and then ground into a fine powder. Cement is the key ingredient in concrete, mortar, and grout. Common types of cement include Portland cement, which is widely used in construction.
-
Concrete: Concrete is a composite material composed mainly of cement, water, and aggregates (such as sand, gravel, or crushed stone). When mixed together in specific proportions, these ingredients form a fluid mass that can be poured, molded, or shaped and then hardens into a stone-like material through a chemical process called hydration. Concrete is used extensively in construction for foundations, driveways, sidewalks, buildings, and infrastructure.
Key Differences:
-
Composition: Cement is an ingredient of concrete, while concrete is a finished product made from a mixture of cement, water, and aggregates.
-
Function: Cement acts as a binding agent that holds the components of concrete together, while concrete provides structural strength and durability for construction applications.
-
Usage: Cement is primarily used in the production of concrete but also has applications in mortar (used for masonry) and grout (used for filling gaps).
In summary, while cement and concrete are related materials in construction, they serve distinct purposes and are not interchangeable terms. Understanding this distinction helps in accurately describing and discussing construction materials and processes.
​
How long does a concrete driveway, patio or sidewalk typically last?
A concrete installations can typically last anywhere from 20 to 40 years or more, depending on various factors such as:
-
Quality of Installation: Properly prepared subgrade, adequate thickness, reinforcement (if used), and proper curing all contribute to the longevity of the driveway.
-
Climate and Weather Conditions: Freeze-thaw cycles, extreme heat, heavy rainfall, and exposure to chemicals (like de-icing salts) can affect the durability of concrete.
-
Maintenance: Regular maintenance such as sealing, cleaning, and repairing cracks or damage can significantly extend the lifespan of a concrete driveway.
-
Load and Use: The frequency and weight of vehicles using the driveway can impact its wear and tear. Heavy vehicles or frequent heavy loads may accelerate wear compared to lighter use.
-
Quality of Concrete: The quality of the concrete mix used and adherence to recommended practices during installation can affect the driveway's durability.
In summary, with proper installation, regular maintenance, and favorable environmental conditions, a concrete driveway can last several decades. Homeowners can enhance longevity by addressing maintenance needs promptly and ensuring the driveway is constructed to withstand the specific demands placed on it.
​
What is the standard slab thickness of a residential interior concrete floor?
The standard slab thickness for a residential interior concrete floor is typically 4 inches. This thickness provides adequate strength and support for the weight of the building and typical household activities, while also being cost-effective. Proper subgrade preparation, including compaction and moisture control, and the use of reinforcement materials like wire mesh or rebar, can enhance the performance and durability of the concrete slab, ensuring a stable and long-lasting floor.
What is the standard slab thickness of a residential concrete garage floor?
The standard slab thickness for a residential concrete garage floor is typically 4-6 inches. This range provides sufficient strength to support the weight of vehicles and withstand the additional stresses associated with garage use, such as the movement of cars, light trucks, and occasional heavy loads. A 4-inch slab is generally adequate for standard passenger vehicles, while a 6-inch slab is recommended for heavier vehicles or more frequent use. Proper reinforcement with rebar or wire mesh, along with well-prepared subgrade and proper drainage, ensures the garage floor's durability and longevity.
What is the standard slab thickness for a sidewalk?
A 4-inch thickness is standard for sidewalks because it provides adequate strength and durability for pedestrian traffic. This thickness supports the weight of people, bicycles, and light maintenance equipment without cracking. It balances cost-effectiveness and performance, using enough material to ensure longevity while keeping construction expenses reasonable. Proper subgrade preparation, including compaction and moisture control, enhances the concrete's performance, preventing issues like settling and cracking. Reinforcement with materials such as wire mesh can further increase the sidewalk's durability, ensuring a long-lasting, safe walking surface for everyday use.
What is the standard slab thickness used for a concrete driveway?
A 4 or 6 inches thick concrete slab is commonly used for driveways due to a combination of durability, strength, and cost-effectiveness. This thickness provides a robust foundation capable of withstanding the weight of typical vehicles, such as cars, SUVs, and light trucks, which exert significant pressure on the driveway surface.
​
Concrete's inherent strength allows it to endure repeated stress from vehicle loads without cracking or deteriorating quickly. A 4 inch thickness is generally sufficient for residential driveways that accommodate passenger vehicles. For heavier loads, such as RVs or delivery trucks, a 6-inch thickness is recommended to provide additional strength and reduce the risk of damage.
Another important factor is the balance between cost and performance. Concrete is more expensive than other materials like asphalt, but its longevity and low maintenance requirements make it a cost-effective choice over time. A 4 or 6 inch slab optimizes material usage, providing sufficient strength without unnecessary expense.
​
Additionally, proper subgrade preparation, including compaction and drainage, enhances the concrete's performance, preventing issues like settling and water damage. Reinforcement with materials such as rebar or wire mesh further increases the concrete's durability.
​
What is the standard size rebar used to construct a 4-inch concrete driveway?
In the construction of a 4-inch concrete driveway, the standard size of rebar (reinforcing bar) used is typically #3 (3/8 inch diameter) or #4 (1/2 inch diameter) rebar. These sizes are commonly used to provide reinforcement within the concrete slab to help control cracking and increase its strength.
Key points regarding rebar in a concrete driveway:
​
-
Purpose: Rebar helps to distribute loads evenly across the concrete slab, reducing the likelihood of cracking due to shrinkage or settling.
-
Placement: Rebar is typically placed in a grid pattern throughout the driveway area, usually with spacing between bars determined by engineering recommendations or local building codes.
-
Installation: Before pouring the concrete, rebar is positioned on a base layer of compacted aggregate and secured in place with wire ties or other fastening methods. It should be positioned at the midpoint of the slab's thickness to be most effective.
-
Size and Quantity: The size (#3 or #4) and quantity of rebar used depend on factors such as the anticipated loads, soil conditions, and local building codes. Engineering specifications may dictate specific requirements for reinforcement.
By incorporating rebar into the construction of a concrete driveway, you can enhance its durability and longevity, especially in areas prone to heavy traffic or soil movement. Professional guidance or consultation with a structural engineer may be beneficial to ensure proper reinforcement based on your specific project requirements.
​
What is the standard size rebar used to construct a 4-inch concrete foundation?
The standard size rebar used to construct a 4-inch concrete foundation is typically #4 (1/2-inch diameter) rebar. This size provides adequate strength and reinforcement for most residential and light commercial foundations.
​
Key considerations for rebar in a 4-inch concrete foundation:
​
-
Purpose: Rebar is used to reinforce the concrete foundation, helping to distribute loads and resist cracking caused by settlement or soil movement.
-
Placement: Rebar is placed in a grid pattern within the foundation footing and sometimes vertically within the foundation walls, depending on structural requirements and local building codes.
-
Spacing and Quantity: The spacing and quantity of rebar are determined based on engineering calculations, taking into account factors such as soil conditions, building loads, and structural requirements.
-
Installation: Rebar should be positioned correctly and secured in place using wire ties or other fastening methods before pouring the concrete. It should be placed at the proper depth within the foundation to provide effective reinforcement.
In summary, #4 rebar is commonly used for reinforcing a 4-inch concrete foundation due to its strength and ability to withstand typical residential and light commercial building loads. Professional guidance from a structural engineer or adherence to local building codes may be necessary to ensure proper reinforcement based on specific project requirements.
​
What is the standard size rebar used to construct a 4-inch thick concrete patio?
The standard size rebar used to construct a 4-inch-thick concrete patio is typically #3 rebar, which has a diameter of 3/8 inch. This size provides sufficient reinforcement for most residential patio applications.
​
Key considerations for rebar in a 4-inch-thick concrete patio:
​
-
Purpose: Rebar helps to prevent cracking and increase the overall strength and durability of the concrete patio.
-
Placement: Rebar is typically placed in a grid pattern throughout the patio area. The spacing between rebar and the quantity used depends on factors such as anticipated loads, soil conditions, and local building codes.
-
Installation: Before pouring the concrete, rebar is positioned on a base layer of compacted aggregate or soil and secured in place with wire ties or other fastening methods. It should be positioned near the midpoint of the concrete slab's thickness to be most effective.
-
Size and Quantity: While #3 rebar is common for residential patios, the size and quantity of rebar may vary based on specific project requirements and engineering recommendations.
By incorporating rebar into the construction of a 4-inch thick concrete patio, you can enhance its strength and longevity, especially in areas subject to heavy foot traffic or where soil movement is a concern. Consulting with a professional or following local building codes can ensure proper reinforcement for your patio project.
​
Is an exposed aggregate concrete driveway more expensive than a standard concrete driveway
Yes, an exposed aggregate concrete driveway is generally more expensive than a standard concrete driveway. The higher cost is due to several factors:
​
-
Materials: Exposed aggregate involves the use of special decorative aggregates, which can be more expensive than the materials used in standard concrete.
-
Labor: The installation process for exposed aggregate is more labor-intensive. It requires additional steps, such as washing away the top layer of cement paste to reveal the aggregates and often more careful handling to achieve the desired appearance.
-
Finishing: Achieving a consistent and attractive exposed aggregate finish requires skilled workmanship, adding to the overall cost.
-
Sealing: Exposed aggregate driveways often need to be sealed to protect the surface and enhance the appearance, adding to the maintenance cost.
Cost Comparison:
​
-
Standard Concrete Driveway: Typically ranges from $4 to $8 per square foot, depending on the location, quality of materials, and local labor rates.
-
Exposed Aggregate Driveway: Can range from $8 to $15 per square foot or more, reflecting the additional materials, labor, and finishing processes involved.
While more expensive, an exposed aggregate driveway offers enhanced aesthetic appeal and can be more slip-resistant, making it a popular choice for homeowners looking to improve the curb appeal and functionality of their driveways.
​
What is the recommended compressive strength of a concrete driveway, patio or sidewalk? (Measured by pounds per square inch or PSI)
The recommended compressive strength of a concrete driveway is typically 3,000 to 4,000 pounds per square inch (PSI). This range provides adequate durability and load-bearing capacity for residential driveways, ensuring they can withstand the weight of vehicles and resist weather-related damage. For driveways that will experience heavier loads, such as RVs or large trucks, a higher compressive strength of up to 4,500 PSI might be recommended to ensure greater durability and longevity. Patios, Sidewalks or non weight bearing slabs will use 3500 psi.Proper curing and reinforcement, along with well-prepared subgrade, are also essential to achieving and maintaining the desired compressive strength.
​
How long should concrete cure before cars are parked on it?
A concrete typically needs to cure for at least 7 days.. However, the curing time can vary based on several factors:
​
-
Weather Conditions: Curing time can be affected by temperature, humidity, and weather conditions. Warmer temperatures generally promote faster curing, while colder temperatures can slow down the curing process.
-
Concrete Mix Design: The specific mix design of the concrete, including the type of cement and additives used, can influence curing time. Some concrete mixes may require longer curing periods to achieve sufficient strength.
-
Thickness of the concrete: Thicker concrete sections may require longer curing times compared to thinner sections.
-
Traffic Load: While light foot traffic may be permissible after 24-48 hours, heavy vehicles such as cars should wait at least 7 days to prevent damage to the concrete during its initial curing phase.
General Guidelines for Curing:
​
-
First 24-48 Hours: Keep the driveway moist and protect it from drying out too quickly. This can be done by covering it with plastic sheeting or using a curing compound.
-
After 7 Days: Concrete typically achieves sufficient strength to support normal vehicular traffic. However, full curing continues over time, reaching optimal strength after approximately 28 days.
-
Avoid Heavy Loads: To minimize the risk of cracking or damage, avoid placing heavy loads or turning vehicles sharply on the driveway during the initial curing period.
It's important to follow specific recommendations from your concrete contractor or consult local guidelines and best practices for curing concrete driveways, patios or sidewalks. Properly cured concrete ensures durability and longevity, maintaining the integrity for years to come.
​
What is the ideal outdoor temperature for pouring concrete flatwork (driveways, patios, etc.)?
The ideal outdoor temperature for pouring concrete flatwork such as driveways and patios is typically between 50°F to 80°F (10°C to 27°C). Concrete sets and cures best within this temperature range because:
​
-
Setting Time: Concrete sets more predictably and uniformly in moderate temperatures, neither too cold to slow the hydration process nor too hot to cause rapid drying.
-
Curing: Proper curing is essential for concrete strength and durability. Moderate temperatures help maintain ideal conditions for curing without excessive heat that can lead to cracking or drying too quickly.
-
Workability: Concrete is easier to work with and finish in moderate temperatures, allowing for smoother surfaces and better finishing results.
​
​Additional considerations:
-
Temperature Fluctuations: Avoid pouring concrete when temperatures are expected to fluctuate dramatically within a short period, as this can affect curing and potentially cause cracking.
-
Protection from Elements: Ensure protection from direct sunlight, wind, and rain during and immediately after pouring to maintain optimal conditions for curing.
By pouring concrete in the recommended temperature range and taking appropriate precautions, you can help ensure a strong, durable, and aesthetically pleasing finished product for your driveway, patio, or other outdoor flatwork.